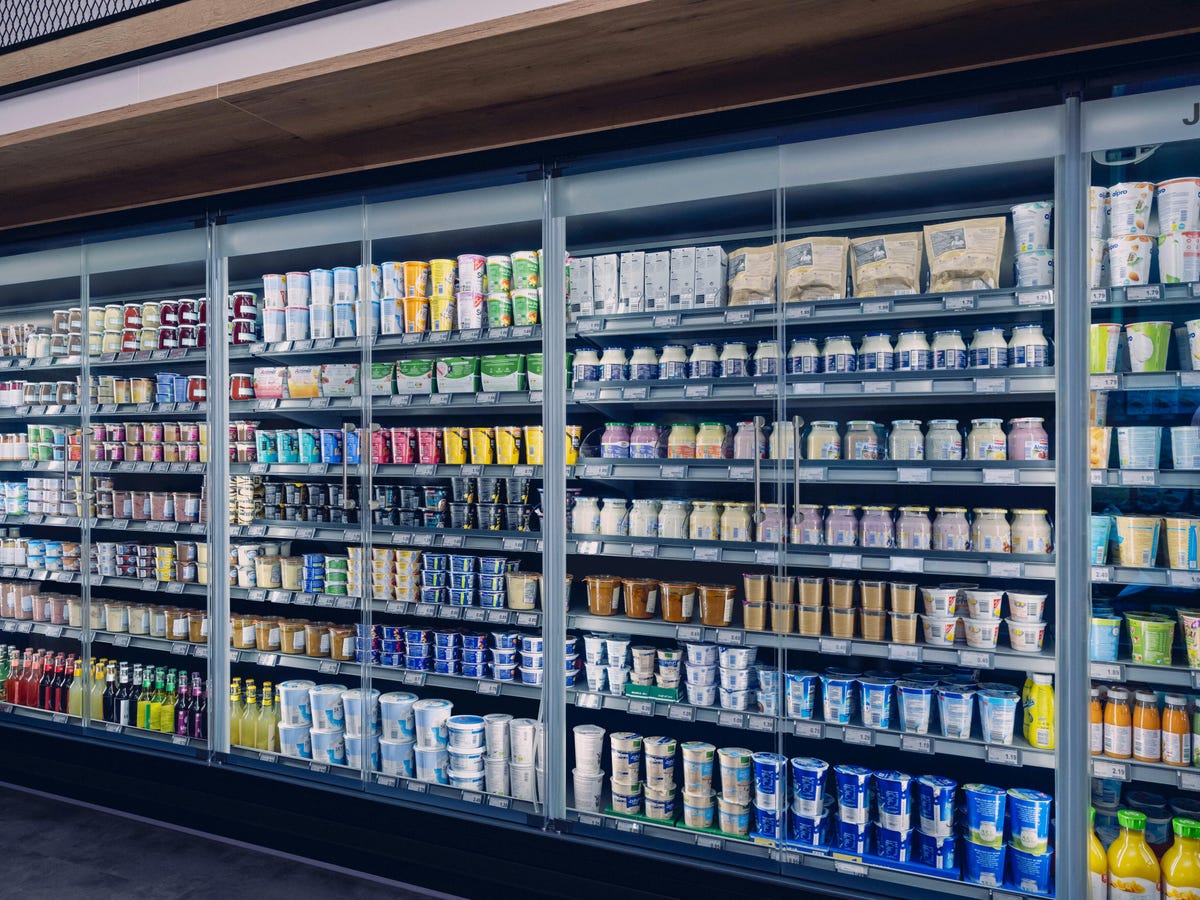
Case Study Co-operative Group
Key Advantages: More Efficient, Lighter and Quieter
One of the key features of the new system is the significantly slimmer design of the refrigerant circuit. The innovative technologies employed in the new system have allowed Copeland to forget the use of numerous additional components often used to increase efficiency in CO₂ systems, such as parallel compressors to recirculate the flash-gas. During the trial run in Malmesbury, perfectly matched components enabled the Copeland CO₂ scroll booster system to reach the level of efficiency achieved by parallel compression systems.
The compact design has also led to major reductions in the size and weight of the system. The CO₂ scroll booster system weighs around 60 percent less than similar products. In total, it weighs around 600 kg less than a comparable solution using conventional technology. The space-saving construction and low weight facilitate installation where space is limited, such as on the roof, which is often the only option at many stores. An added plus: The new system is much quieter than the refrigeration system with reciprocating compressors previously installed at the Malmesbury store.
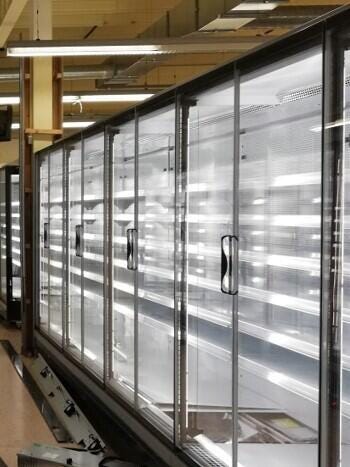
During the trial run that spanned 18 months in total, the system provided reliable cooling performance from the word go during the hottest summer in the northern hemisphere (June to August 2020) since records began. Photo: Copeland.
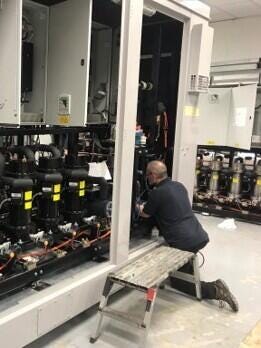
Based on the result of the 18-month trial run, The Co-operative Group has decided to gradually install the Copeland CO₂ scroll booster system at several other stores. Photo: Copeland.